CARBURISING
Carburising is a surface hardening process widely used in industries such as automotive, aerospace, and heavy machinery to improve the wear resistance and fatigue strength of steel components. The process involves diffusing carbon into the surface layer of low-carbon steel, creating a hard “case” while retaining a tough and ductile “core.” This combination of properties is essential for components subjected to high surface stresses, such as gears, shafts, and bearings. However, improper execution of the carburising process can lead to a failure mode known as case crushing, where the hardened case cracks or spalls under mechanical stress. Understanding the causes and prevention strategies for case crushing is crucial for ensuring the reliability and longevity of carburised components. [1][2]
The surrounding external environment provides the diffusing factors for the job being heat treated. Diffusion elements are added to the furnace’s surroundings through the use of liquid or gaseous media that carry the elements in the atomic stage. Then, under the thermal action at the operation temperature, which is above the A3 temperature of the steel for carburising and below the A1 temperature for nitriding, these elements in their atomic form diffuse onto the surface of the steel. Extra alloying elements diffuse over the surface, causing a significant change in composition from the bulk with desired chemical properties, as seen in carburising or nitriding processes. Nitriding eliminates the need for this kind of hardening, whereas the carburized surface of steel needs it in order for martensite formation to occur and provide the necessary hardness. Since nitride production, which can occur at the temperature of nitriding operation, is the only phase change associated with the nitriding process.[2]
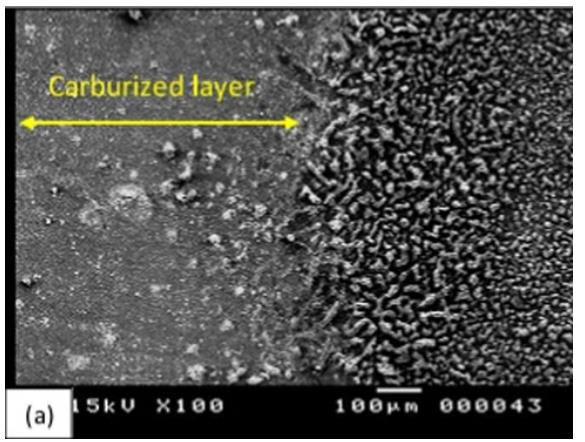
Figure 1 SEM micrographs showing microstructures of carburized case depth for 6h [6]
Causes of Case Crushing
Insufficient Case Depth: One of the primary causes of case crushing is an insufficient case depth. A thin carburised layer lacks the necessary support to withstand surface stresses, making it prone to cracking and failure. During service, the surface layer experiences high stress concentrations. If the case is too thin, it cannot adequately distribute these stresses, leading to micro-cracking and eventual failure. Proper control of the carburising parameters, such as temperature, time, and carbon potential, ensures adequate case depth. [1] Mandal (2015) stresses the importance of process optimization to achieve the desired case properties. [2]
Improper Carbon Content: Excessive or uneven carbon distribution can result in a brittle case, which is susceptible to cracking under stress. High carbon content can lead to the formation of brittle carbide phases, such as cementite, which reduce the toughness of the case. Additionally, an uneven carbon gradient can cause differential thermal expansion during cooling, leading to residual stresses. Using precise control of the furnace atmosphere and maintaining a consistent carbon potential can help achieve uniform carbon distribution. [1] Parrish (1999) highlights the need for accurate carbon control to prevent the formation of brittle phases. [3]
Residual Stresses: Residual stresses arise from the differential expansion and contraction of the case and core during heating and cooling. During the quenching phase of carburising, rapid cooling can induce tensile stresses in the case, leading to crack initiation. If these stresses exceed the material’s tensile strength, case crushing occurs. Controlled cooling rates and the use of appropriate quenching media can reduce residual stresses. Post-quenching tempering is also recommended to relieve stresses and stabilize the microstructure. [1][3]
Overloading and Mechanical Stress: Mechanical overloading, either during operation or due to poor design, can lead to case crushing. When the applied stresses exceed the load-bearing capacity of the carburised layer, the case can crack or spall. This is particularly prevalent in components with high surface loads or impact stresses. Designing components with sufficient case depth and considering operational loads during the design phase can mitigate the risk of overloading. Mandal (2015) suggests that careful consideration of the mechanical design is essential for preventing case failure. [2]
Effects of Case Crushing
Case crushing has several detrimental effects on the performance and lifespan of carburised components. Reduced Load-Bearing Capacity: Crushing of the case significantly decreases the component’s ability to bear loads, leading to mechanical failure under operational conditions. Components with reduced load-bearing capacity are more prone to failure under cyclic or impact loading, leading to premature wear and potential catastrophic failure. Mandal (2015) notes that maintaining a balance between hardness and toughness is crucial for optimal load-bearing performance. [2]
Increased Wear and Fatigue: A compromised case is more susceptible to wear and fatigue, reducing the component’s service life. Cracked or spalled surfaces exhibit increased friction and wear, accelerating degradation and necessitating more frequent maintenance or replacement. Parrish (1999) emphasizes that maintaining surface integrity is key to preventing accelerated wear and extending component life.[3]
Loss of Surface Integrity: The integrity of the surface layer is compromised, leading to accelerated degradation and potential failure in critical applications. Surface integrity is critical for maintaining the component’s functionality and aesthetic appearance. Loss of integrity can lead to further damage and reduced performance. Proper maintenance of the case-core relationship is vital for preserving surface integrity, as discussed by Mandal (2015). [2]
Prevention Strategies
Optimizing Carburising Parameters: Controlling carburising parameters such as temperature, time, and carbon potential is essential for achieving the desired case properties. Use precise process control and monitoring to maintain consistent carburising conditions. Advanced control systems and monitoring equipment can help achieve optimal results. [1][2] Parrish (1999) and Mandal (2015) both emphasize the importance of process control in achieving desired case characteristics. [3]
Post-Treatment Processes: Post-treatment processes such as shot peening can introduce beneficial compressive stresses on the surface, reducing the likelihood of case crushing. Employ shot peening or other surface modification techniques to enhance surface properties and reduce tensile residual stresses. Mandal (2015) discusses the benefits of post-treatment processes in enhancing the durability of carburised components. [2]
Material Selection: Choosing steels with appropriate alloying elements can enhance hardenability and reduce the risk of case crushing. Select materials with alloying elements such as chromium, molybdenum, and nickel to improve hardenability and support the carburised case. Parrish (1999) highlights the role of material selection in achieving desired mechanical properties. [3]
Design Considerations: Designing components with adequate support for the carburised case and considering operational loads during the design phase can mitigate the risk of case crushing. Incorporate stress analysis and simulation tools to evaluate component performance under expected loading conditions. Mandal (2015) emphasizes the importance of design considerations in preventing case crushing and enhancing component performance. [2]
Case crushing in carburising is a complex phenomenon influenced by various factors, including case depth, carbon content, residual stresses, and mechanical loading. Understanding these factors and implementing appropriate prevention strategies is crucial for ensuring the reliability and longevity of carburised components. By optimizing carburising parameters, selecting suitable materials, and considering design factors, engineers can effectively mitigate the risk of case crushing and enhance the performance of carburised components. [1][2][3]
REFERENCES
[1] Parrish, Geoffrey. “Carburizing: Microstructures and Properties.” ASM International, 1999.
[2] Mandal, S.K. “Heat Treatment Of Steels.” McGraw Hill India, 2015.
[3] Davis, J.R. “Surface Hardening of Steels: Understanding the Basics.” ASM International, 2002.
[4] Totten, G.E. “Steel Heat Treatment: Metallurgy and Technologies.” CRC Press, 2006.
[5] ASM International Handbook Committee. “Metallography and Microstructures.” ASM Handbook, Volume 9, 2004.
[6 ] Saleh, B., & Ahmed, S. M. (2013). Slurry Erosion–Corrosion of Carburized AISI 5117 Steel. Tribology Letters, 51(1), 135–142