Aluminum Welding: Clean Surfaces, Strong Connections
The importance of proper cleaning to remove oxide and surface contaminations from aluminum pieces to be welded cannot be over-emphasized. Hydrogen and oxygen will cause porosity and dross respectively in welds. Oil or grease films contain oxygen and hydrogen and if left on edges to be welded, these will cause unsound welds with reduced mechanical and electrical properties.[1]
Aluminum must be cleaned before welding in order to ensure structural integrity of the finished product. To successfully clean the surface of aluminum, you need to do the following two things:
1. Use an organic solvent, like acetone, or a mild alkaline solution, such a strong soap, to remove oil, grease, and water vapor. Citrus-based degreasers can also be used, but before welding, make sure the item is rinsed and dried.
2. Use a strong alkaline or acid solution or a stainless steel wire brush (exclusively for aluminum) to remove surface oxides. Oxide-removal solutions are available in spray or squeeze bottles from many welding providers for on-site use. Handle these solutions with extreme caution, and remember to rinse and dry the part before welding.
According to first part, after processes the oil, grease and water may stick through surface and cause damage after welding. So that before welding this contaminations should be cleaned very carefully to achieve welding with one piece and succesfully.
In second part, for aluminum, oxide thin film tend to formed in room temperature. That’s make welding process is not suitable with thin film. Aluminum have low melting point 660°C, high oxide layer (Al2O3) have melting temperature of 2300°C. And this oxide layer have porous structure. After welding, porous structure formed and that makes welding process very fragile and unnecessary. Below micrographs showed us how aluminum formed with and without oxide layer and that micrographs give us ability to know the quality of our welding process.
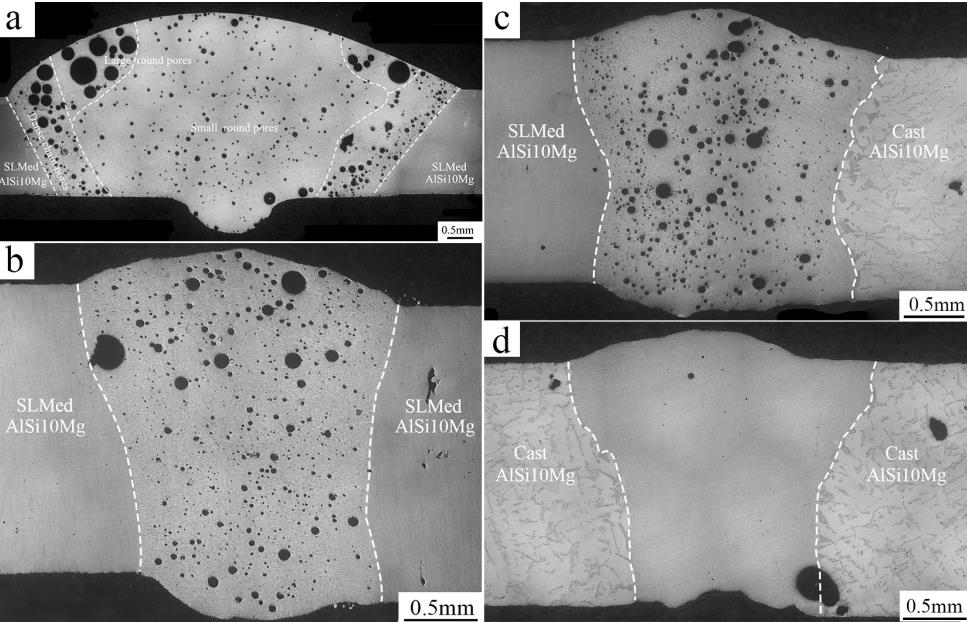
Figure 1: cross-section morphology of the welds.[2]
As it can be seen in micrographs, aluminum without cleaning (with oxide layer) have porous structure. Furthermore that porous structure make welding fragile. Just the opposite applied process with cleaning showed up very pure and one piece. Cracks are preferentially formed at the maximum stress pore and propagate to adjacent pores. Cracks propagate along with pores in large stress in the matrix. Thus a deflected crack can be seen in the cross section, which crosses lots of dense pores.
A common pitfall in part cleaning is improper handling after cleaning and before welding. It is recommended that lint-free gloves be used instead of rubber gloves and that parts be stored in clean areas. Part protection materials and fixturing should be compatible with the parts, as an example; many metals contaminate refractory metal weld joints, contact with copper, brass or lead can contaminate stainless steel and lead to cracking. [3]
Suggested cleaning methods include grinding, wire brushing, or needle scaling on heavy materials; using solvents to clean grease and oil; and using a noncontaminating stainless wire brush or a nonmetallic foam disk to clean aluminum and milling. Because cleaning is difficult to remove from aluminum without reducing the metal thickness, consideration should be given to anodizing the base plate and stud after the welding operation.[5]
Suggested cleaning methods include grinding, wire brushing, or needle scaling on heavy materials; using solvents to clean grease and oil; and using a noncontaminating stainless wire brush or a nonmetallic foam disk to clean aluminum and milling. Because anodizing is difficult to remove from aluminum without reducing the metal thickness, consideration should be given to anodizing the base plate and stud after the welding operation. Common cleaning techniques include abrading the surfaces by grinding, grit blasting, or wire brushing; pickling or chemical descaling; and vapor degreasing. In some cases, the ends of the workpiece must be machined or ground to fit the dies, particularly in welding of rough forgings or castings. Also, a chamfer may be required on the ends of the workpiece to initiate flashing action. Die burns, upset slippage, and inferior welds may be caused by poor fit-up between the current-conducting dies and the workpiece. [5]
Wire brushing generally is not always recommended, because contaminants may become embedded in the metal surface. Acetone is preferred for cleaning electron gun components and workpiece parts. If workpieces are cleaned in chlorine or other halogen-containing compounds, residue from these compounds must be removed by another cleaning method (usually thorough washing in acetone) before welding.[4]
CHEMICAL CLEANING
Surface Cleaning
Prior to coating and/or welding, machined base-metal surfaces are usually degreased by a multiple step procedure.
⦁ Wash with abrasive detergent followed by a hot-water rinse
⦁ Rinse in deionized water
⦁ Ultrasonically clean in ethyl alcohol
⦁ Blow dry using inert gas
For other fabrication methods, such as electrodeposited interlayers or foils, the base metal surfaces are degreased prior to plating or joining to remove organic surface films that would otherwise degrade the metallic bonding at the interlayer/base-metal interfaces.[4]
Cathodic Cleaning
Cathodic cleaning occurs when a metal surface is bombarded with a stream of positive gas ions if ( 1 ) the workpiece is at a negative potential with respect to the electrode , and ( 2 ) argon or other heavy inert gas is used to shield the arc . Cathodic cleaning is evident as a bright , clean area on either side of the weld bead . be used to remove surface oxides and films of ad- sorbed gases on the metal surface . Cathodic cleaning can be observed when welds are made with the following processes :
(1 ) Direct current , reverse polarity gas tungsten – arc
(2 ) Alternating – current gas tungsten- arc ( reverse – polarity cycle only )
( 3 ) Direct current , reverse polarity , gas metal arc
( 4 ) Direct current , reverse polarity , plasma arc .
The mechanism that produces cathodic cleaning is sputtering . Atoms or groups of atoms can be ejected from a surface as the result of impact by positive ions . Once free from the surface , the sputtered atom diffuses through the gas in contact with the surface ( room air or shielding gas ) .[1]
MECHANICAL CLEANING
Although mechanical methods are less widely used than chemical methods, they are usually preferred for removing heavy scale, and they can be indispensable in removing the more tenacious lubricants, such as a pigmented drawing compound. Mechanical methods are also useful in surface preparation that involves abrading or roughening, which may be required on a very smooth surface to promote wetting and filler-metal flow.
Mechanical cleaning includes the following methods:
⦁ Grit and shotblasting
⦁ Mechanical sanding and grinding
⦁ Filing and hand sanding
⦁ Cleaning with steel wool
· Wire brushing and scraping
For best results, cleaning should extend beyond the joint area. Shot or steel gritblasting is often effective and is preferable to sandblasting because it avoids the embedding of silica particles on the surface, which interferes with the flow of solder. Mechanical cleaning is not recommended for softer metals, such as copper.[4]
REFERENCES
[1] Welding of Aluminum and Aluminum Alloy, R. P. Meister, David Carl Martin
[2] ZHANG, Changchun, et al. A comparison between laser and TIG welding of selective laser melted AlSi10Mg. Optics & Laser Technology, 2019, 120: 105696.
[3] Recommended Practices for Electron Beam Welding and Allied Processes 4th Edition Supersedes, An American National Standard, AWS C7.1M/C7.1:2013
[4] WELDING, BRAZING, AND SOLDERING WAS PUBLISHED IN 1993 AS VOLUME 6 OF THE ASM HANDBOOK. THE VOLUME WAS PREPARED UNDER THE DIRECTION OF THE ASM HANDBOOK COMMITTEE.
[5] About weldability and welding of Al alloys: case study and problem solvingE. Fracchia, F. Gobber, M. Rosso Department of Applied Science and Technology, Politecnico di Torino, Duca degli Abruzzi, 24, 10129 Torino, Italy